Artículo N.º 632111
Aglomerante pigmentado a base de agua y recubrimiento de base
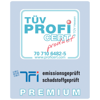
Características del producto
Los valores mencionados representan las características típicas del producto y no deben entenderse como especificaciones vinculantes del producto.
Alcance
- Imprimación en los sistemas de difusión de vapor de agua (WDD) de Remmers
- AW_GR_55
- AW_GR_56
- Imprimación en sistemas aprobados por el DIBt para salas comunes (aprobación de la inspección general de edificios Z-156.605-1414)
Propiedades
- EG_GR_10
- EG_GR_47
- Permeable al vapor de agua
- Resistente a la congelación/descongelación
- EG_GR_48
- Libre de agentes suavizantes, libre de nonilfenol y alquilfenol
- En estado reactivo no causa daños fisiológicos
-
Programación de operaciones
-
Requisitos para el sustrato
El fondo deberá estar firme, rígido, libre de partículas sueltas, polvo, aceites, grasa, marcas de goma y otras sustancias que puedan afectar la adherencia del producto.
La resistencia a la abrasión del fondo deberá ser en promedio al menos 1,5 N/mm² (el valor individual más pequeño al menos 1,0 N/mm²), la resistencia a la compresión al menos 25 N/mm².
Al aplicarse en el sistema OS 8, la resistencia a la abrasión del fondo deberá ser en promedio al menos 2,0 N/mm² (el valor individual más pequeño al menos 1,5 N/mm²).
Disponible informe de inspección sobre el comportamiento de la unión ante la presencia de humedad posterior según DIN EN 13578 en el sistema OS 8.
Los fondos tienen que haber alcanzado su humedad de equilibrio y además estar protegidos de la humedad posterior durante la aplicación.
hormigón máx. 6 % en masa de humedad Pavimento cementoso máx. 6 % en masa de humedad U1_B_35
El poder adhesivo de la superficie imprimada tiene que ser en pro medio al menos 1,5 N/mm² (mínimo valor indivdual al menos 1,0 N/mm²), la resistencia de compresión tiene que ser al menos 25 N/mm².
Consultar las indicaciones detalladas en la ficha técnica actual del producto respectivo.
-
Preparativos
Preparar el sustrato con medios adecuados, por ejemplo, granallado de acero, de modo que cumpla con las especificaciones indicadas anteriormente.
Rellenar las imperfecciones en el fondo con sistemas Remmers PCC o con morteros Remmers EP.
-
-
Preparación
-
Contenedores combinados
Adicionar toda la cantidad de endurecedor (comp. B) a la masa base (comp. A).
Mezclar a continuación la masa con un agitador eléctrico de marcha lenta
(aprox. 300 - 400 r.p.m.) .Pasar la mezcla a otro recipiente y volver a mezclar a fondo.
Hay que mantener un tiempo de mezclado mínimo de 3 min.
Si se forman estrías ello es indicio de un mezclado insuficiente.
ZBK_B_12
-
Tratamiento
-
Las altas temperaturas acortan, mientras que las bajas temperaturas – especialmente con una alta humedad del aire – alargan por lo general los tiempos de espera indicados.
-
Herramientas / Limpieza
-
Encontrará datos exactos en el programa de herramientas de Remmers.
Limpiar con agua los instrumentos de trabajo inmediatamente después de utilizarlos.
Durante la limpieza hay que aplicar medidas de protección y eliminación adecuadas.
-
Almacenamiento / Vida útil
-
Mín. 9 meses en el envase original no abierto, en lugar fresco, seco y protegido contra las temperaturas bajo 0.
-
Ejemplos
-
Capa de imprimación
Aplicar el material sobre la superficie. Con los medios adecuados, por ejemplo una escobilla de goma, repartir y acabar con un rodillo de resina epoxi, asegurándose que los poros del fondo sean completemente tapados.
De ser necesario aplicar varias capas.
-
Capa de nivelación / compensación de la porosidad
El consumo depende de la condición del sustrato.
-
Recubrimiento
El consumo depende de la condición del sustrato.
-
Capa base para recubrimientos esparcibles
La capa de base, aún fresca, se espolvorea con un exceso de arena de cuarzo o copos de coloruro o sedimento.
Luego del endurecimiento, eliminar el excedente
A continuación, aplique la fijación o el sellador de cabeza correspondiente al sistema.
-
-
Información general
-
Todos los valores y consumos especificados fueron determinados en condiciones de laboratorio (20 °C) con tonos de color estándares. Estos valores pueden variar según el caso de aplicación.
¡Las capas de imprimación deberán ser aplicadas siempre tapando los poros! Se podrá dar el caso que las cantidades de consumo se eleven. Eventualmente deberá aplicarse una segunda capa de imprimación.
Tratar superficies adyacentes solo con productos con el mismo número de lote, ya que de otra manera podrán presentarse ligeras diferencias en el color, el brillo y la estructura.
Los tonos débiles (p.e. amarillo, rojo o naranja) del sellado aplicado posteriormente tienen – según nuestra experiencia – un efecto de barniz. En este caso serán necesaria la aplicación de una capa adicional del color que compagine, p.e. gris luminoso.
H_B_50
H_B_51
Para lograr superficies lisas deberá considerarse las profundidades de rugosidad.
Generalmente, las resinas epoxi no presentan un color estable bajo la influencia del temporal y de la radiación ultravioleta.
En las fichas técnicas correspondientes y en las recomendaciones de Remmers podrá encontrar más indicaciones acerca de la aplicación, estructuras y cuidados de nuestros productos.
En el caso de los sistemas OS 8 deberán respetarse los manuales de ejecución
Para la instalación de sistemas sujetos a homologación, deben respetarse las indicaciones contenidas en la homologación correspondiente.
-
-
Instrucciones de eliminación
-
Eliminar las grandes cantidades de restos del producto de acuerdo con las normativas aplicables en el envase original. Reciclar los envases después de haberlos vaciado completamente. Este producto no debe eliminarse junto con la basura doméstica. No introducir en el alcantarillado. No vaciar al desagüe.
-
-
Seguridad / Normativa
-
¡Sólo para aplicadores industriales!
Encontrará más información detallada sobre la seguridad durante el transporte, almacenamiento y manipulado, así como sobre la eliminación y ecología, en nuestra Hoja de datos de seguridad actualizada y en el folleto „Resinas epoxi en el ramo de la construcción y medio ambiente” (Deutsche Bauchemie e.V., segunda edición, año 2009).
-